PRODUCT
PROCESSING
All processes are demanded to
numerical control machinery, but every single piece receives a
peculiar handcrafted care
in the finishing process, mechanical adjustments and, most of all,
regarding the sharping which is thoroughly performed by hand.
The choice in materials is the best among what the market offers, which
contributes in giving high performance to our products.
Our products are not art pieces, they're simple and efficient
professional technical instruments.
Our
production
Extrema Ratio produces tactical
knives, that is fixed blade or openable knives for severe use.
The use of special steels, of polymers like KRATON and of processes
like vacuum hardening, make our knives the best cutting instruments.
Care in details, like stainless steels screws, detachable handles,
technical scabbards equipped with belts and extensions make these
instruments the top. This quality results in the adoption of these
instruments by important operative army units.
Potentiality
As
said, Extrema Ratio is a mechanical workshop, therefore we can
virtually face the production of mechanical and plastic instruments.
We have chosen to take in charge the production of tactic knives but
the white weapons license of production and the techical qualification
for the production of common and war weapons held by the two partners
open unlimited horizons in the blade production field. We can thus
produce double edged blades, bayonets, automatic knives and swords.
The
present working area enables us to face production orders both of bulk
quantities and of small amounts (50-100 pieces), upon request from
military units.
CHARACTERISTICS
& MATERIALS
The blades
At present our blades are produced using only N690, a steel martensitic
enriched with chrome, vanadium, molibdene and cobalt, from the finest
homogeneity it is transformed in plate for a crossed lamination/rolling.
Naturally we make the most of nearly ten years experience of using this
steel, it is treated with all the expedients and processes which give
it the maximum in quality. Cutting by high power laser, vacuum thermo
treatment, special sand blasting.
It is protected through burnishing and carbonitruration which can
satisfy the most demanding military specifications. For our entire
production, both military and civilian. This Austrian stainless steel
has resulted in an outstanding combination of strength and flexibility.
All this comes at a very accessible price.
Our ambition is not the perfect blade; our target is to offer our
military customers a functional and efficient blade for a wide range of
uses. With this kind of steel we are rewriting the European military
standards regarding blades. Furthermore all our blades are hand
sharpened, in order to obtain a tough, enduring and efficient
sharpness, which is substantially different to that obtained by
industrial methods.
Handles
for fixed blades
In collaboration with the faculty of Motor Sciences at Perugia
University we have developed the ERMH. This handle lends itself
superbly for both work and combat.
The grip is formed in a hollow which thins the handle and furnishes a
firm grasp for the three stronger fingers of the hand (which make up
the opposing force ).
The handle is asymmetric but straight, which allows for
a dynamic shift from "saber" to "reverse" while leaving the end of the
tang free as a rope guide or for use as a blunt instrument. It is
suitable for hands of all normal dimensions, male or female, and for
use with thermal gloves.
It is a single piece, easy to dismantle, allowing for excellent
ordinary or extraordinary maintenance.
It is produced through a "Forprene" injection, a polymer with extreme
temperature resistance (-40 / +120), thus reaching the requirements for
NATO standards.
Some models, such as the "back up", use the same handle in "ERMH C",
which is more compact, more useful for dissimulation and with low risk
of entanglement: the minimum requirement for a firm grasp.
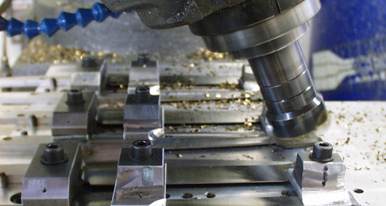
Fixed blade sheaths
Particular attention has been paid to the development of sheaths which
are, like the handle, the interconnection between the blade and the
user.
The fixed blade and bayonet sheaths have two retaining systems, both of
which can be used ambidextrously.
The first is located inside the hard part of the sheath, it is a
pressure mechanism to avoid losing the knife in case of rolling or
being overturned, the second is a lace with two buttons to fix the
blade handle close to the body, this prevents it becoming entangled
with vegetation, with other equipment (like the rifle sling) or - in
the case of parachuting - with the static line or parachute cord.
It can be carried comfortably and silently.
Its insertion is facilitated by a wide safety opening giving easy
access for replacing the knife when the user cannot see the sheath due
to it being covered by equipment or other gear such as an ammo pouch.
The hard sheath prevents the misplacement of the blade
in case of shock, and aids fast drying, thanks to a drainage hole,
reducing exposure to elements that favour the oxidation process.
The soft part of the sheath is provided with several
points for connection with equipment, an extension and two thigh straps
with elastic and Velcro fixings are included with the sheath. Many of
the sheaths are provided with a fixing system compatible with "spring"
systems.
The straps and all the accessories are in nylon, all buttons
and metallic parts are made from burnished brass or have a polymer
cover.
The semi-rigid sheaths, like those of the bayonets or the KS,
KL, KH, are made in nylon or Cord mixed with closed cell polymeric
sponge that does not absorb humidity and water.
Folding Knives
For
the handle we use Anticorodal, an aluminium alloy with superior
mechanical characteristics and a remarkable resistance to oxidization.
The Anticorodal pieces are burnished through a high level of anodized
oxidation.
The metal parts are made from N690 (like the blade) when a high level
of hardness is required, AISI 304 e AISI 303 where high resistance
against oxidation is needed (screws, pivots, turnings).
Steel parts are burnished either through carbonitrading (with
zirconium) or according to military specifications.
The springs are made in stainless steel burnished with the same
procedures.
The ergonomics of the sheath follow the same standards of the fixed
blade knife, however in this case the lowered surface on the handles
makes the thumb-stud reaching simpler.
Most of the folding knives are provided with a glass
shattering nodule, or in the case of folding knives for heavy work,
they have a protuberance in tempered steel which is attached to the
back of the sheath.
We use only tested blade blocking systems such as "back lock" or "liner
lock".
TEST
To obtain the development of
products with a high level of performance, our prototypes and samples undergo
the strictest NATO tests, integrated with other more specific
and even stricter tests carried out inside our laboratory.
To ensure a real and absolute
efficiency, we execute comparative tests with the
most representative products from other firms in this sector.
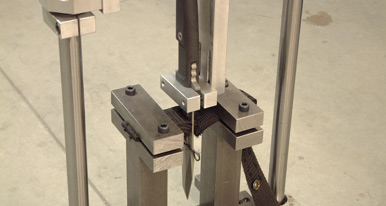
The capacity to
perforate is
measured by a machine of our own production, calibrated by an
electronic dynamometer on the average force applied by a man of medium
build.
The material used for this test is one or more NATO standard belts and
soft ballistic protection.
These tests have given interesting results regarding the
characteristics and the phenomenon connected with the perforation
capacity.
The same machine can be used for testing the blade efficency.
The falling tests
concern the robustness of the tips and tangs (for the bayonet we also
test the lug mechanism on the rifle).
The test involves dropping the knife from both positions from a
pre-established height inside a Plexiglas tube, which prevents the
knife from rotating without slowing the rapidity of its descent.
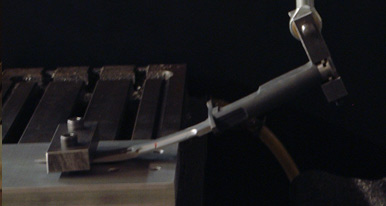
The flexibility and
resistance tests
are carried out using the electronic dynamometer which highlights the
load in kg on the product, fixed at both ends with opposing movement on
two different levels.
We calculate the limit of the elastic deformation and the breaking
point.
The oxidation tests are
carried out with the collaboration of the Florence University
of Engineering.
These tests comprise exposure to a saline fog in a controlled
atmosphere according to the time and percentage required by NATO
standards.
The electro miographic
test regarding ergonomics are made in collaboration with the Faculty
for Motor Sciences at Perugia University.
These tests take into consideration the pressures and possible
discomfort arising from a prolonged use of the blade as a work tool,
the hold and stability of the handle.
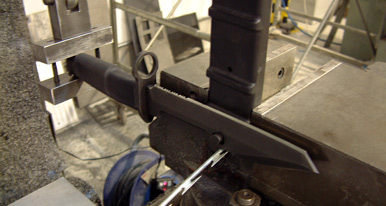
In case of accessories such
as the concertina wire cutter
on the bayonets we proceed by testing as vast as possible a range of
wires, until the product passes all of the possible tests.
|